Optimizing Your Welding WPS: Techniques for Improved Performance and Performance
Optimizing Your Welding WPS: Techniques for Improved Performance and Performance
Blog Article
Opening the Power of Welding WPS: Methods for Performance and Safety in Manufacture
In the realm of fabrication, Welding Treatment Specifications (WPS) stand as the backbone of welding operations, dictating the needed actions for achieving both efficiency and security in the construction process. Understanding the intricacies of WPS is extremely important to using its full potential, yet several organizations struggle to unlock truth power that exists within these records (welding WPS). By diving right into the approaches that maximize welding WPS, a globe of enhanced performance and heightened security awaits those happy to explore the nuances of this essential facet of construction

Significance of Welding WPS
The value of Welding Treatment Requirements (WPS) in the manufacture industry can not be overemphasized. WPS function as an essential roadmap that lays out the essential steps to make sure welds are executed consistently and properly. By defining important criteria such as welding processes, materials, joint layouts, preheat temperatures, interpass temperatures, filler steels, and post-weld warm therapy demands, WPS offer a standardized technique to welding that improves effectiveness, quality, and safety in manufacture procedures.
Adherence to WPS aids in achieving uniformity in weld quality, lowering the probability of flaws or architectural failures. This standardization also facilitates compliance with market guidelines and codes, guaranteeing that made frameworks satisfy the needed safety criteria. In addition, WPS documents enables welders to duplicate successful welding treatments, leading to consistent results across different tasks.
In essence, the meticulous growth and strict adherence to Welding Procedure Specifications are paramount for upholding the integrity of welded structures, guarding versus prospective threats, and promoting the track record of construction business for providing top notch product or services.
Key Elements of Welding WPS
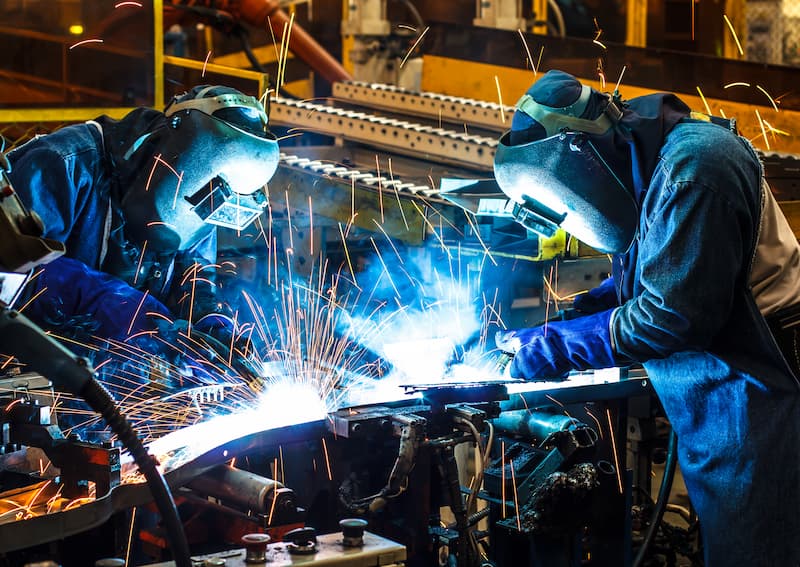
Enhancing Effectiveness With WPS
When optimizing welding procedures, leveraging the crucial elements outlined in Welding Procedure Requirements (WPS) becomes crucial for making the most of and simplifying procedures productivity. One method to boost performance with WPS is by meticulously choosing the appropriate welding parameters. By adhering to the certain standards offered in the WPS, welders can guarantee that the welding devices is set up properly, causing constant and top notch welds. Furthermore, following the pre-approved welding sequences outlined in the WPS can considerably reduce the moment invested in each weld, eventually increasing overall performance.
Additionally, proper training and accreditation of welders in understanding and implementing WPS can additionally improve performance. Making certain that all team participants are skilled in analyzing and carrying out the WPS precisely can rework and reduce mistakes, conserving both time and sources. Regularly evaluating and updating the WPS to integrate any type of lessons learned or technological advancements can also contribute to effectiveness enhancements in welding operations. By welcoming the guidelines set forth in the WPS and constantly seeking methods to maximize processes, makers can achieve greater performance degrees and superior outcome.
Ensuring Safety And Security in Manufacture

Making certain security in fabrication includes a complex approach that encompasses various facets of the welding procedure. Welders must be equipped with appropriate gear such as helmets, handwear covers, and safety apparel to mitigate dangers connected with welding activities.
Additionally, adherence to correct air flow and fume extraction systems is vital in maintaining a healthy job setting. Welding fumes include harmful substances that, if breathed in, can posture significant health risks. Applying effective air flow procedures helps to lessen direct exposure to these harmful fumes, advertising breathing health amongst workers.
Routine devices maintenance and evaluations are likewise vital for making sure safety in construction. Faulty equipment can cause injuries and mishaps, highlighting see here the value of routine checks and prompt repairs. By focusing on precaution and fostering a society of awareness, fabrication centers can develop a safe and secure and effective workplace for their personnel.
Implementing WPS Ideal Practices
To enhance operational effectiveness and make sure top quality results in fabrication procedures, integrating Welding Treatment Specification (WPS) ideal methods is extremely important - welding WPS. Applying WPS ideal methods includes thorough preparation, adherence to industry standards, and constant monitoring to guarantee ideal outcomes. First of all, choosing the proper welding process, filler product, and preheat temperature level specified in the WPS is critical for achieving the wanted weld top quality. Secondly, guaranteeing that certified welders with the essential certifications perform the welding treatments according to the WPS guidelines is essential for uniformity and dependability. Regularly upgrading and examining WPS files to show any kind of procedure renovations or adjustments in products is likewise an essential best practice to keep precision and importance. Additionally, supplying comprehensive training to welding workers on WPS check demands and ideal practices cultivates a culture of safety and security and quality within the construction setting. By vigilantly applying WPS ideal techniques, makers can simplify their procedures, lessen mistakes, and deliver exceptional items to fulfill client assumptions.
Conclusion
In verdict, welding WPS plays a crucial role in guaranteeing efficiency and safety in manufacture procedures. By adhering to these strategies, businesses can unlock the complete potential of welding WPS in their fabrication operations.
In the realm of fabrication, Welding Procedure Specs (WPS) stand as the foundation of welding procedures, dictating the essential actions for achieving both performance and safety and security in the construction procedure. By defining essential parameters such as welding processes, materials, joint designs, preheat temperature levels, interpass temperature levels, filler steels, and post-weld warmth treatment requirements, WPS provide a standard strategy to welding that enhances performance, top quality, and security in fabrication processes.
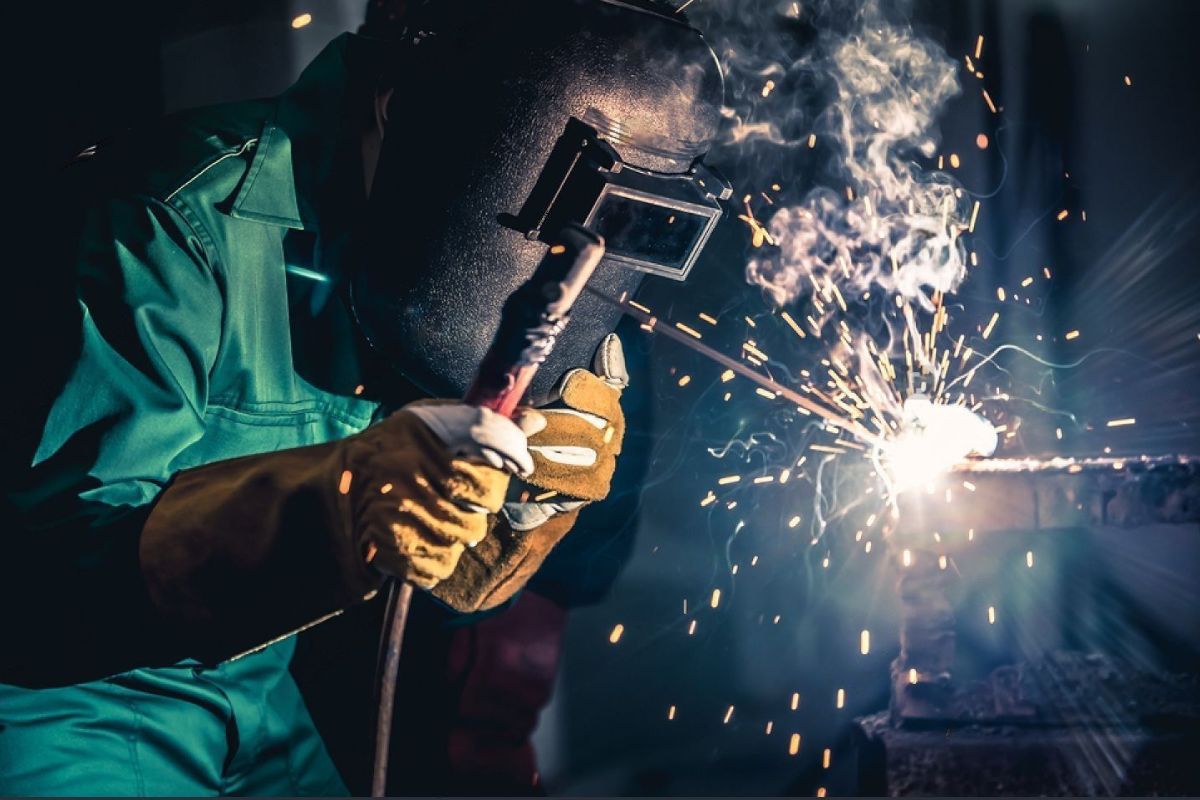
When optimizing welding operations, leveraging the vital elements detailed in Welding Treatment Specifications (WPS) comes to be necessary for enhancing processes and optimizing performance. (welding WPS)
Report this page